RECOVERY PUMPS: HYDROCARBON VAPOR RECOVERY SYSTEMS

Our STAR recovery pumps are designed for n-Butane and Butane/Propane blends. They are an engineered unit delivering safety and performance perfection resulting in high quality results both in product output and operational costs. The STAR hydrocarbon vapor recovery pump systems are ergonomic, durable, and simple to maintain.
All of our STAR pumps are engineered, manufactured, and come with the best customer support out of Oregon, USA. These vapor recovery units are professionally engineered and certified to the NFP58 fire codes and standards and are for use in the following approved states: Arizona, Arkansas, California, Colorado, Florida, Idaho, Illinois, Kansas, Kentucky. Louisiana, Maine, Maryland, Massachusetts, Michigan, Minnesota, Montana, Missouri, Nebraska, Nevada, New Mexico, New York, North Carolina, North Dakota, Ohio, Oklahoma, Oregon, Pennsylvania, South Dakota, Texas, Utah, Vermont, Washington, Washington D.C., Wyoming.
​
In today’s business climate, cutting operational costs while maintaining legislative adherence is more important than ever, especially within the Botanical and Cannabis industry. For facilities with high usage of fuels, vapor recovery is not only required by law but also an effective way to reduce material and financial waste. Vapor recovery ensures that harmful materials are not released into the atmosphere or product, and most people have seen this type of system every time that they fill up a car’s gas tank. While there are a variety of vapor recovery systems available, here at PDX.Gold we offer our Solvent Transfer and Recovery (STAR) pump systems.
​
Need help deciding which unit is best for you? Let’s talk, call us at 1-503-783-6550 and we’d be happy to consult which equipment is best for your business needs.
​
We also offer free vapor recovery pump demos for our STAR units all the time! If you're outside the Pacific Northwest (PNW), we are more than happy to arrange freight. Click the link below to submit a demo request to get your hands on our superior technology in vapor recovery systems.
The VaporSMARTZ iQ150 Solvent Transfer And Recovery pump is the most advanced technology from PDX.Gold and is a potent addition to any processing lab. This powerful system has the “smarts” to help keep your process on track and pairs perfectly with the industry’s leading hydrocarbon extraction systems by decreasing your recovery times and increasing your profits instantly.
​
Built for the professional extractor, the recovery pump automatically shuts off when the output pressure exceeds designed limits - typically when the system is incorrectly configured (closed valves, etc.), cooling needs to be increased post recovery or when there is inadequate volume in the solvent recovery tank. The pump also shuts off when drawing excessive vacuum - typically when the system is incorrectly configured or when the cycle has ended and there's no more solvent to recover. The pump will also shut off if the drive motor draws an excessive amount of current - which may indicate contamination has affected the compressor. These features help the operator find and solve issues BEFORE they cause damage to the recovery pump or other parts of the extraction system – saving YOU time and money.
​
Our ergonomic design also provides a usable work surface at standard counter height within the extraction lab with no bending down to check gauges.


- Butane/Propane/Blends
​
- Rated to 150 psi
​
- Recovery rate of 2+ lbs/min.
​
- 2 HP, UL & NEMA 7 rated motor
​
- 15 CFM
​
- Safety Assurance: Automatic shut off system
- Explosion Proof: All control enclosures are NEMA 7, class 1, Division 1 rated
​
- Ergonomic Design: Standard counter height with built-in work station
​
- Stainless Steel fittings and PTFE Teflon lined stainless steel braided hoses
​
- 3rd party engineering certified. Every purchase comes with a full certification report upon request
​
​
​
​
FEATURES:
​
- Propane/Blends
​
- Rated to 150 psi
​
- Recovery rate of 2+ lbs/min.
​
- 2 HP, UL & NEMA 7 rated motor
​
- 6.5 CFM free air flow
- Explosion Proof: All control enclosures are NEMA 7, class 1, Division 1 rated
​
- Stainless Steel fittings and PTFE Teflon lined stainless steel braided hoses
​
- Footprint: 30" x 18" x 16"
​
- 3rd party engineering certified. Every purchase comes with a full certification report upon request
​
​
​
​
​
.png)
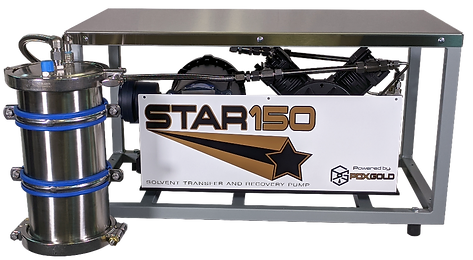
FEATURES:
​
- Propane/Blends
​
- Rated to 150 psi
​
- Recovery rate of 2+ lbs/min.
​
- 2 HP, UL & NEMA 7 rated motor
​
- 6.5 CFM free air flow
- Explosion Proof: All control enclosures are NEMA 7, class 1, Division 1 rated
​
- Stainless Steel fittings and PTFE Teflon lined stainless steel braided hoses
​
- Footprint: 28.25" x 18.5" x 25.25"
​
- 3rd party engineering certified. Every purchase comes with a full certification report upon request
​
​
​
​
​
.png)

We also offer free vapor recovery pump demos for our STAR units all the time!
If you're outside the Pacific Northwest (PNW), we are more than happy to arrange freight. Click the link below to submit a demo request to get your hands on our superior technology in vapor recovery systems.
For centuries, nutritional and medicinal benefits have been provided by plant compounds. Over time, the healing properties of plants has been scientifically researched, which has led to botanical oil extraction. Currently, botanical oil extraction is an emergent commodity, especially because science has continued to learn of additional benefits plant compounds provide, including medicinal, recreational, healing, and soothing benefits. As more people learn of these benefits, there is a stronger demand for the ability to extract botanical oils on a larger scale.
​
Cannabis has become increasingly popular regarding botanical oil extraction. Cannabidiol (CBD), tetrahydrocannabinol (THC), and terpenes are common compounds separated from the cannabis plant, often using hydrocarbon extraction. Although ethanol and carbon dioxide (CO2) extraction methods are also used, here at PDX.Gold, our experience shows hydrocarbon is a more widely used recovery process due to its effectiveness of extracting terpenes (without post processing), efficiency and cost.
​
Continue reading to learn more about hydrocarbon vapor recovery systems, how the units work, the hydrocarbon extraction process in 4-steps, and the uses of vapor recovery pumps.
What is a Vapor Recovery Unit?
​
Vapor recovery is the process of removing vapors from storage units to keep compounds pure and safe for use. A vapor recovery unit part of a system that removes unwanted vapors from containment units, such as collection vessels and hydrocarbon tanks. Closed Loop Extraction vapor recovery units are generally composed of three major components: a gas compressor, a drive motor, and a switch gear (optional). Vapor recovery units use gas compression and suction to remove vapors found in sealed containers or to transfer solvent from one container to another. Closed Loop Extraction units should have a filter-dryer (aka scrubber) to prevent any organic material or moisture from reaching the solvent transfer and recovery pump and damaging it or transferring contaminants to the recovery tank.

How Vapor Recovery Systems Work
​
A vapor recovery system uses a gas compressor to create pressure differentials which move gasses between containers. Closed Loop Extraction units usually have three types of pressurized containers – soaking column(s), collection vessel and source / recovery tank(s).
In a closed loop hydrocarbon extraction system, plant material (cannabis, hemp, lavender, etc) is soaked in a liquid organic solvent (typically butane, propane or a blend of the two). This is to draw (extract) botanical oils and other beneficial compounds from the source plant material. A solvent transfer pump is used to fill the soaking column(s) containing the plan material with solvent. After a soak period, where the botanical oils diffuse into the organic solvent, the solvent / oil mixture is drawn off from the plant material to a collection vessel. This collection vessel is heated very slightly (usually to less than 100ËšF) to raise the vapor pressure of the solvent. At this point the Solvent Transfer and Recovery pump is engaged to recover the solvent and transfer the solvent vapor to a recovery tank for re-use. This process continues until over 99.5% of the solvent has been removed from the collection tank – leaving the desired oils & compounds in the collection vessel. The soaking column is cleaned and refilled with plant material and the process is repeated.
The hydrocarbon extraction process is a direct, efficient 4-step process that produces a high-quality product. Before beginning the process, it’s best to ensure the plant material hasn’t been exposed to harsh elements, such as excessive heat, ultraviolet rays, etc. Ideally, the plant material should be stored in a vacuum-sealed environment that is dark with a stable temperature.

Hydrocarbon extraction: A 4-Step Process
Soak the plant material:
Cold organic solvent is flushed through the soaking column and over the plant material. Allowed to soak in the solvent for a short period, this step dissolves the cannabinoids and terpenes into the solvent, and the solution can be processed.
​
Remove the impurities:
Further refinement of the solution can be done in this second step. Waxes and lipids get may be removed from the solution through a winterization trapping process, which uses jacketed columns cooled with super-chilled solvent or dry ice to lower the solvent / oil temperature and solidify unwanted waxes & lipids. Once chilled, the solution passes through filters that separate the waxes and lipids from the chilled solution.
​
Collection of Concentrate:
After all impurities are removed, the concentrated solution passes into a separate container, often called a collection vessel, where any residual solvent remaining is removed. The isolated solvent moves back into the recovery / source tank to remove most of the solvent from the solution.
​
Purification:
There are varying methods that allow for further purification, which include the following:
-
Vacuum Purging – removing residual solvents using a low-pressure low-heat oven cycle.
-
Co-solvent Separation – isolating one or more cannabinoids by matching varying solvents to cannabinoid polarity.
-
Co-solvent Crystallization – isolating cannabinoids through crystallization by matching varying solvents to cannabinoid polarity.
-
Centrifugal Terpene Removal – separating terpenes from the primary extract through the use of a centrifuge device.
​
Need help deciding which unit is best for you?
Let’s talk, call us at 1-503-783-6550 and we’d be happy to consult which equipment is best for your business needs.
We also offer free vapor recovery pump demos for our STAR units all the time! If you're outside the Pacific Northwest (PNW), we are more than happy to arrange freight. Click the link below to submit a demo request to get your hands on our superior technology in vapor recovery systems.
​